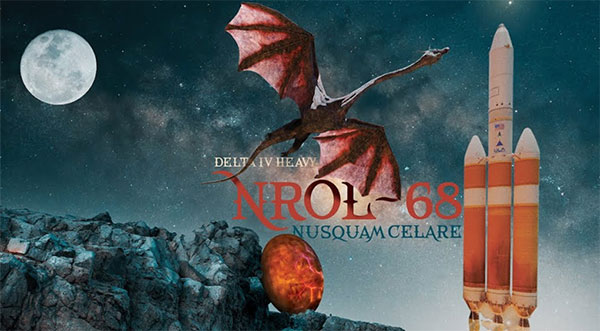
Production welding is critical in various industries, serving as the backbone of many manufacturing processes. From medical device manufacturing to general and industrial applications and gun component manufacturing, the demand for high-quality welding services is ever-present.
However, optimizing the welding procedures is crucial to meet industry standards and ensure customer satisfaction. The article focuses on optimization strategies for enhanced welding procedures to meet the highest industry standards and ensure customer satisfaction.
- Process Analysis and Parameter Optimization
Process analysis and parameter optimization involve evaluating and fine-tuning various factors within the welding process to achieve optimal results. It encompasses analyzing welding techniques, heat input, travel speed, filler material selection, and other critical parameters.
Process analysis and parameter optimization are essential for production welding because they directly impact weld quality, productivity, and cost-effectiveness. Just as adjusting the tension of strings and optimizing finger placement produces harmonious sounds, analyzing and optimizing welding parameters result in well-formed, high-quality welds.
Manufacturers can ensure consistent and superior welds by carefully assessing and optimizing these parameters while minimizing defects and rework. However, analyzing and optimizing the welding process requires attention to detail, precision, and fine adjustments to achieve the desired outcome.
- Advanced Welding Equipment and Techniques
Advanced welding equipment and techniques involve utilizing cutting-edge technologies and specialized methodologies to achieve superior results in production welding. That includes integrating high-quality welding machines, advanced power sources, and innovative welding processes such as microlaser beam welding and microscopic TIG (Tungsten Inert Gas) welding.
These techniques offer solutions for complex and delicate welding applications in industries such as microelectronics, medical device manufacturing, and precision engineering. These advanced techniques offer enhanced precision, control, and productivity, allowing for the welding of diverse materials with high accuracy and minimal distortion.
Leveraging a reliable welding company with advanced welding equipment and techniques like Micro Weld, Inc, manufacturers can optimize their welding procedures, improve weld quality, increase efficiency, and expand the range of applications in various industries. That ensures that manufacturers stay at the forefront of technological advancements in welding.
- Welding Automation
Automation is pivotal in enhancing production welding processes across various industries, including general manufacturing, industrial applications, medical device manufacturing, oil and gas, aerospace, and defense. Manufacturers can achieve precise and consistent welds with high repeatability by incorporating robotic systems and CNC (Computer Numerical Control) technology.
Automation improves productivity by reducing human error, increasing production rates, and enabling complex welding operations. It also enhances safety by minimizing worker exposure to hazardous environments. With automation, manufacturers can streamline their welding processes, improve efficiency, and meet the stringent quality standards demanded by diverse industries.
- Process Monitoring and Control
Process monitoring and control involve using various technologies to guarantee excellence in quality and consistency of production welding. That includes real-time monitoring and control systems that track critical parameters such as arc voltage, current, wire feed speed, gas flow rate, and temperature. Advanced sensors, data acquisition systems, and software algorithms enable continuous monitoring and analysis of these parameters.
By closely monitoring the welding process, an experienced company like Micro Weld, Inc can make timely adjustments and corrections to maintain process stability, optimize weld quality, and minimize defects. Process monitoring and control are vital in ensuring quality control, improving efficiency, and meeting industry standards for welding in producing critical components and parts.
- Incorporating Quality Assurance and Non-Destructive Testing (NDT)
Quality assurance and non-destructive testing (NDT) are integral components of the optimization strategies for enhanced production welding procedures. These strategies ensure that welded joints meet quality standards and are defect-free.
By implementing rigorous inspection and testing procedures such as visual inspection, radiographic testing, ultrasonic testing, and magnetic particle testing, a reliable welding company like Micro Weld, Inc can detect potential defects early on, preventing costly rework and ensuring the integrity of welded components.
Quality assurance practices enable continuous improvement, refinement of welding procedures, implementation of corrective actions, and compliance with industry standards. This optimization strategy enhances weld quality, reduces the risk of failures, and ultimately increases customer satisfaction.
Conclusion
Strict adherence to production welding procedures ensures consistent quality, reliability, and safety in welded components. Manufacturers can minimize defects, enhance productivity, and meet industry standards by using quality welding technologies and following established guidelines and protocols.
Adherence to procedures demonstrates a commitment to excellence and instills confidence in customers. It is an essential aspect of successful manufacturing operations, contributing to the overall success and reputation of the company. However, outsourcing to a professional welding company like Micro Weld, Inc is crucial for the quality and consistency of the welds.